Industrie 4.0 – from a perspective of applied research
Reimund Neugebauer, Fraunhofer-Gesellschaft, Germany
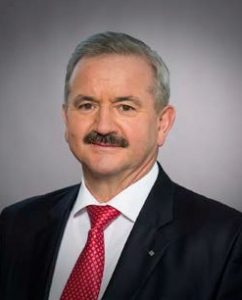
“Industrie 4.0” is about real-time data-exchange between cyber-physical systems with the overall goal to increase productivity, quality and flexibility while lowering costs for personalized products and processes.
Thus, »Industrie 4.0« offers great potential for improving resource efficiency throughout the production process. Developing corresponding technologies to seize this potential and thereby contributing to the conservation of natural resources is one of the main research goals of the Fraunhofer-Gesellschaft.
Enablers for »Industrie 4.0« are advances in computer, network and sensing technologies. The transformation will further progress over the next decades in face of new technologies, innovations and infrastructural settings and enable new kinds of products and business models. The ultimate vision for the factory of the future is based on the smart and digital connection of machines, robots and 3D-printers, products, sensor systems, resource infrastructures, logistics systems and ordering platforms together with humans, cloud systems, intelligent assistants and the internet. Hence, the total sourcing, production, retail, delivery and recycling processes will be regarded as a unified organism.
The new and high degree of digitization requires sophisticated technologies in many areas. These include research and development for e.g. novel forms of cyber security, networks and fast connectivity (5G and beyond) for low latency tactile internet, computing and processing solutions, sensor integration and Machine Learning.
Innovative project examples from these research areas will be shown in the presentation.
Prof. Neugebauer is a Fellow of the International Academy for Production Engineering (CIRP) and a member of the National Academy of Science and Engineering (acatech). From 2010 to 2011 he was the president of the German Academic Society for Produc-tion Engineering and since 2014 he has been a member of Leopoldina – the German National Academy of Sciences. This year, Prof. Neugebauer was appointed co-chair of the German federal government’s High-Tech Forum, an advisory board for the develop-ment of Germany’s research and development policy. As a member of the acatech Inno-vation Dialogue steering committee, the Fraunhofer president engages with Chancellor Merkel and other government representatives as well as with high-ranking representa-tives of science, industry and society on issues of future innovation policy. He is also on the executive board of the newly established “Plattform Industrie 4.0”, an alliance of representatives from politics, industry, associations, science and trade unions.
Technological challenges in Medical Robotics for Surgery and Patient Specific Treatment
Alon Wolf, Technion, Israel
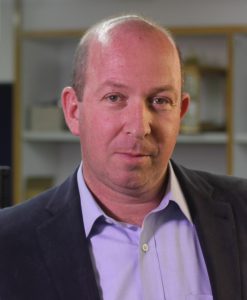
Modern surgery has developed rapidly with the scientific advances of the past century. From pioneering treatments in the battlefield to the creation of academic surgery, modern advances have ushered in new age for surgical interventions, one that has moved past being regarded as just an accessory to medicine and is instead is so far advanced that it stands in a league of its own. In the old days, surgical procedures were performed by barbers who, between haircuts and bloodletting, also performed invasive procedures that in no way resemble what we consider as surgery today. Those invasive procedures were performed in operating rooms once known as operating theatres. The procedures were often performed in front of a live audience while the patient was awake. Now, just a century later, surgery is performed by trained medical doctors and the old operating theaters have been replaced by sterile rooms where robotic systems often perform part of the operation. Indeed, the operating theater is now referred to as the Operating Room of the Future. In recent years even more advanced and futuristic medical technologies have been developed. These technologies – many of them robotics – enable the surgeon to replace biological parts of the human body with smart machines. This new field of Biomedical engineering research has been named Cybernetics.
We must ask ourselves…
When will the day come where man and machine become one? Or are we there already?
Net Positive Manufacturing : A Restoring, Self-healing and Regenerative Approach to Future Industrial Development
Shahin Rahimifard, Loughborough University, England
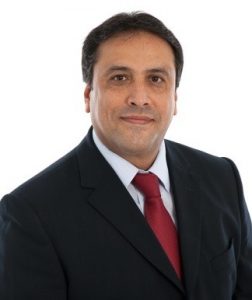
In today’s consumer driven society, manufacturers can exert unparalleled environmental, economic and societal influence, either for good or bad. The recent uncontrolled industrial growth within both developed and developing countries have frequently resulted in significant, and at times irreparable, damage to the environment as well as the health of people in an attempt to sustain economic growth at any cost. In response, global sustainability initiatives, due to inherent and inevitable economic barriers, have often adopted a ‘Less Bad’ approach, which is based on meeting the demands of regional and national legislation and incremental efficiency measures. The benefits of such initiatives are now perceived as too small and too slow to tackle the needs of tomorrow. In this context when ‘Less Bad is Not Good Enough !’, what should our aspirations and goals be beyond the scope of current sustainability strategies, methods, tools and technologies ?
At the heart of the proposed paradigm shift through ‘Net-Positive Manufacturing’ is the ability of manufacturing businesses to adopt a restoring, self-healing, and regenerative approach and simply to put back more into society and the environment than what they take out. Therefore net-positive manufacturing is not just about minimising the negative impacts, but also about redefining and re-structuring manufacturing so that all areas of society and the natural environment are demonstrably enhanced through industrial processes and systems. This radically novel vision for future industrial development presents a number of methodological, organisational, technological, social and ethical research challenges which are explored in this paper.
Shahin Rahimifard is a Professor of Sustainable Engineering at Loughborough University and the Founder and Director of the Centre for “Sustainable Manufacturing and Recycling Technologies (SMART)” [www.lboro.ac.uk/smart], which was established in 2004. His research work is focused on sustainability issues throughout a ‘Product Lifecycle’, including projects on sustainable product design, resource efficient manufacturing, sustainable business models, and reuse and recycling technologies. These projects have benefited from involvement of a number of high profile global manufacturers and retailers, which include Rolls-Royce, Jaguar Land Rover, GM, Nike, Clarks, Next, Unilever, PepsiCo, Marks and Spencer, and Tesco.
Professor Rahimifard is currently the Deputy Director of the UK National Centres for ‘Industrial Sustainability’ and ‘Innovative Food Manufacturing’ in which he is leading a wide range of research projects ranging from ‘design of future smart factories‘ and ‘robotic disassembly and remanufacturing’ to ‘resource efficient localised production of food products’ and ‘valorisation of food waste for human nutrition’.
Professor Rahimifard is the Editor-in-Chief of the ‘International Journal of Sustainable Engineering [www.tandf.co.uk/journals/tsue]’, the inaugural issue of which was published by Taylor and Francis in January 2008.
International Networking in Manufacturing Research and Education: Case Studies and Lessons Learned
Erman Tekkaya, TU Dortmund University, Germany
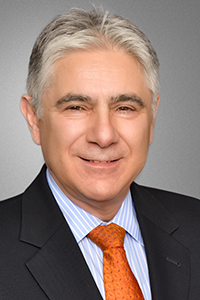
Erman Tekkaya – Full CV
Resilient production – the prerequisite for optimum resource exploitation in smart factories
Matthias Putz, Technische Universität Chemnitz, Germany
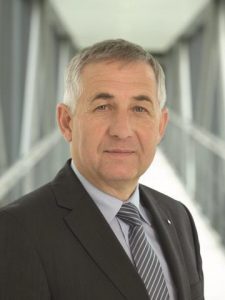
Matthias Putz – Full CV
Towards Nano-manufacturing
Fengzhou Fang, Tianjin University, China
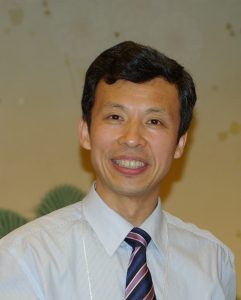
Nanomanufacturing can be further classified as nano precision manufacturing and nano scale manufacturing. Typical examples include nano mechanical machining to realize complex forms in nano precision and focused ion beam fabrication to realize various features in nano scale. To better design and control nano mechanical machining process, it is vital to understand the fundamental mechanism. Since the atomistic details of manufacturing process are difficult to obtain by experiments, molecular dynamics (MD) Simulation as a Simulation method has been widely used to study the machining mechanism. However, the length and time scales that MD can probe are still limited, which prevent MD from modeling the real machining process as it generally involves in nano, micro and macro scales. Therefore, it is essential to develop multiscale method coupling nano, micro and macro scales. This keynote speech overviews the previous multiscale simulations and particularly present a 3D multiscale model to study the nano machining process. The model consists of a single crystal silicon workpiece and a rigid diamond tool. In the critical region around the tool, there are large strain gradients and thus the molecular dynamics is employed. While in the “far-field” region with small strain gradients, Linear elastic FE is adopted. MD and FE are coupled through a handshake (HS) region where MD atoms and FE nodes overlap. Each provides boundary conditions for the other at the edge of the HS region to realize the concurrent multiscale study. Machining of optical freeform elements is presented as the application. The fundamentals of focused ion beam fabrication are also reported as the typical nano scale manufacturing process. As an application of nano scale fabrication, nano optics is discussed, which is the study of the behavior of light on the nanometer scale. A wide variety of novel optical properties would appear in nano-optics, such as, strongly enhanced light transmission, beyond diffraction limitation, etc. With the rapid development of nano-optics, surface plasmon based nano optical elements development have attracted extensive attention, which can be used in the surface plasmon interference nanolithography, plasmon-enhanced sensing and spectroscopy, and super focusing on the nanoscale, etc.
Professor Fengzhou Fang has been working in the field of manufacturing since he became a faculty member at university in 1982. His research interests are in the areas of micro/nano machining, optical freeform manufacturing, bio-medical manufacturing, ultra-precision manufacturing and metrology. He has been invited to deliver over 90 keynote speeches and invited presentations in international conferences and seminars in manufacturing field, and holds more than 50 patents related to manufacturing methods, processes, systems and instruments. Dr. Fang is a fellow of the International Academy for Production Engineering (CIRP), the International Society for Nanomanufacturing (ISNM), and the Society of Manufacturing Engineers (SME). He is the founding president of ISNM, a council member of CIRP, chairman of CIRP Manufacturing Curriculum Committee (MEC), board member of the Asian Society for Precision Engineering & Nanotechnology (ASPEN), and the editor-in-chief of the Nanomanufacturing and Metrology (N&M). He is also a recipient of the SME Albert M. Sargent Progress Award.
Perspectives of International Engineering Education
Holger Kohl, TU Berlin, Germany
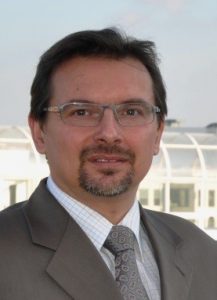
The working environment of young engineers within the dynamic global society and economy is more and more coined by mobility, intercultural exchange and virtual cross-border communication. Young engineers have to work in international and interdisciplinary teams. They have to communicate with colleagues, suppliers, and customers from all over the world as well as from different cultural backgrounds. Moreover, global companies require engineers to independently develop and manage product, process, and business model innovations by pursuing an entrepreneurial mindset.
For coping with the global working challenges of these young engineers, the keynote outlines perspectives for international engineering education. A novel inter-university engineering curriculum is presented, focusing on action-based teaching and learning in transnational and interdisciplinary teams of students. The curriculum fosters the development of entrepreneurial initiatives by leading the students through the development phases of an evolving start-up company.
Subsequently, a use case based on a master course which has been jointly established in cooperation by four different European universities is showing the potential of the inter-university engineering curriculum. Learning objectives for the master course aimed at raising the awareness about sustainable value creation by addressing the development of sustainable and technological innovations with entrepreneurial objectives.
Holger Kohl – Full CV
Sustainable Re-configurable Manufacturing Systems
Yoram Koren, The University of Michigan, USA
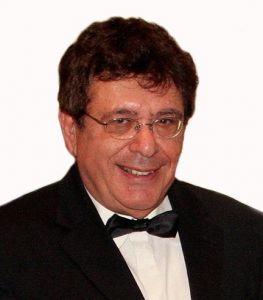
Technological advances and continued globalization have led to rapidly changing markets where consumers are demanding more and more individualized/customized products at short delivery times and lower costs. With increasing constraints being placed on the relentless consumption of resources, meeting the demands of rapidly changing markets present technological challenges. Thus, to be profitable and to generate sustainable value for all stakeholders, manufacturers must develop capabilities to rapidly and economically respond to changing market needs while at the same time minimizing adverse impacts on the environment and benefiting society.
Reconfigurable Manufacturing Systems (RMS) and its characteristics of scalability, convertibility, diagnosability, customization, modularity and integrability provide the capability to quickly adjust production processes to meet market needs.
This paper examines the significance of developing next generation manufacturing systems for low-volume manufacturing by adapting RMS characteristics with sustainable manufacturing implementation.
Prof. Yoram Koren is internationally known as “The Father of Reconfigurable Manufacturing Systems.” In 1995, in a proposal to the US NSF, he conceived the RMS science base, principles and characteristics, and was awarded $47 million by the NSF and private industries to develop the RMS paradigm. He is the inventor of 7 patents encompassing RMS technologies. Koren’s 1999 CIRP keynote paper on RMS is the most cited paper of all CIRP publications (1,800 citations).Yoram Koren is a Distinguished University Professor Emeritus of Manufacturing at the University of Michigan, in Ann Arbor. Professor Koren is a Member of the US National Academy of Engineering. He is a Fellow of CIRP (since 1982), a Fellow of SME, a Fellow of ASME, and a Fellow of IEEE. During his career he received 20 major awards and honors.
Professor Koren has a B.Sc. and M.Sc. in Electrical Engineering, and D.Sc. in Mechanical Engineering from the Technion – Israel Institute of Technology. He had academic appointment at the Technion, McMaster University in Canada, the University of Wisconsin, Madison, and he joined the University of Michigan as a professor of Mechanical Engineering in 1985.
Professor Koren is the author of four original books: Numerical Controlled Machine Tools (1978), Computer Controlled Manufacturing Systems (1983) – an award winning book that it is still being published, Robotics for Engineers (1985) which was translated by the publisher (McGraw Hill) to Japanese and French, and The Global Manufacturing Revolution (2010) which was published by Wiley. Koren has published 300 papers that have 24,000 citations and h-index 67 (per Google Scholar). He is the inventor of 14 U.S. patents in CNC, Robotics, and RMS technologies. His inventions have been implemented in the U.S. automotive manufacturing industry.
Additive Manufacturing technologies: present and future
Paulo Bartolo, Manchester University, England
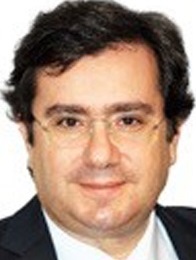
Additive Manufacturing, a group of processes that create products by adding material in a layer-by-layer way, is a key technology for the development of smart factories marked by a shift towards a physical-to-digital-to-physical connection. This keynote reviews the most recent developments in this field in terms of materials and fabrication processes and discusses the use of additive manufacturing for product design and its relevance for industrial sectors such as aerospace and aeronautics, automobile, construction, railway and medical. The concept of 4D Printing to produce morphing structures and the fabrication of functionally graded structures are also outlined. Finally, other emerging application areas are presented and major challenges and opportunities discussed.
Prof. Paulo Bartolo holds a PhD degree in Polymer Physics from the University of Reading (UK, 2001), a Master of Science in Mechanical Engineering (1996) and a Licenciatura in Mechanical Engineering (1993), both from the Technical University of Lisbon (Portugal).
Paulo Bartolo is Professor of Advanced Manufacturing Processes at the Polytechnic Institute of Leiria (Portugal), Adjunct Professor at Queensland University of Technology (Australia), Visiting Professor at Nanyang University (Singapore), and Professor of Biomaterials (Catedra UNESCO) at the University of Habana (Cuba).
He is a CIRP (The International Academy of Production Engineering) member, Vice-Chairman of the CIRP Scientific Technical Committee on Electro-Physical and Chemical Processes, GARPA (Global Alliance of Rapid Prototyping Associations) Portuguese Representative and Member of the Direction Board of the International Society of Biomanufacturing, Scientific advisor of the Research Institute in Biofabrication (BIOFABRIS) funded by the Brazilian Government and regional coordinator of the working group of Rapid Manufacturing Platform.
He was member of a Commission appointed by the Portuguese Parliament to prepare a Portuguese Strategic Plan for Science & Research (2010-2011). He also was the Director of the Centre for Rapid and Sustainable Product Development, Polytechnic Institute of Leiria, Portugal, a Centre of Excellence in Mechanical Engineering of the Portuguese Foundation for Science and Technology and Vice-Chairman of the CIRP Collaborative Working Group on Biomanufacturing (2010-2012), Coordinator of the Iberoamerican Network on Biomanufacturing (BIOFAB Network), funded by CYTED (2008-2010). This research network engaged more than 200 researchers from 20 Universities and Research Institutes in Argentina, Brazil, Cuba, Mexico, Paraguay, Portugal, Spain and Venezuela. Paulo Bartolo has been member of the evaluation panels of several International funding agencies, such as the Portuguese Foundation for Science and Technology (Portugal), the Portuguese Agency for Innovation (Portugal), the Italian Agency for the Evaluation of Universities and Research Institutes (Italy), Reumafonds, the Dutch Arthritis Association (The Netherlands), Fonds Wetenschappelijk Onderzoek (FWO), the Flanders Research Foundation (Belgium), the Natural Sciences and Engineering Research Council of Canada (Canada), the Swiss National Science Foundation (Switzerland), the Flanders Strategic Initiative Materials (Belgium), and the South Africa Science Foundation (South Africa).
High-pressure thermo-chemical recuperation – a way toward sustainable propulsion systems
Leonid Tartakovsky, Technion, Israel
To meet GHG emission targets and to decrease oil dependency, overall energy consumption of road vehicles must be substantially reduced. Various types of propulsion technologies are under consideration, like internal combustion engine (ICE), hybrid electric (HE), plug-in hybrid electric (PHE), range extended electric (REE), electric battery, fuel cell, etc. The article provides a comparison of various propulsion technologies and arrives to the conclusion that internal combustion engines (ICEs) will be a major propulsion option in the foreseen future with massive penetration of hybrid vehicles to global markets. Utilization of more energy-efficient ICEs together with low-carbon-intensity fuels is, therefore, of great importance on a way toward development of sustainable propulsion systems. About one-third of fuel energy introduced to ICE is wasted with engine exhaust gases. A promising way of engine’s waste heat recovery is by using the energy of the exhaust gases to sustain endothermic reactions of fuel reforming. This approach is called Thermo-Chemical Recuperation (TCR).
We go beyond the previous studies in this field by applying direct injection of the reformate gas together with the high-pressure steam-reforming process. We aim at developing a high-pressure TCR-ICE set as a part of a series hybrid propulsion system, thus alleviating the acute problems of the reformer’s startup and transient behavior. The obtained experimental results showed that engine energy efficiency is improved by 18%-39% (higher values at lower loads) and pollutant emissions are reduced by 73-94%, 90-96%, 85-97%, 10-25% for NOx, CO, HC and CO2 emissions, respectively, compared with gasoline in a wide power range, without any need in exhaust gas aftertreatment.